Mini-ALTO: An update from Simon
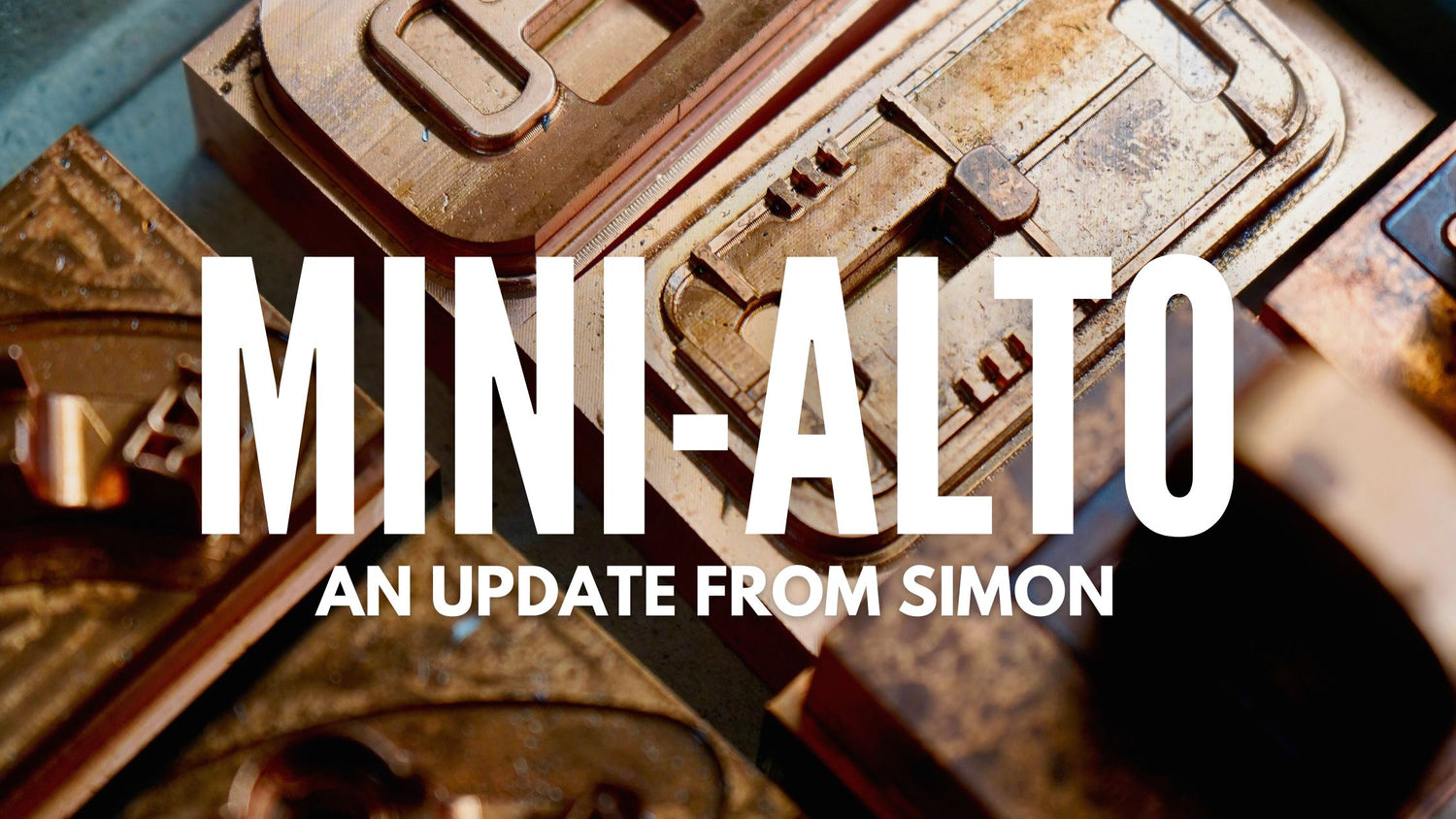
It's not all smooth sailing...
Since we started Radius Windshields last year, we’ve tried to be as open as possible with the development process of our products.
One of the obvious Pro’s to our openness is that everyone can see what we are doing and how things are progressing. However…. one of the Con’s is that everyone can see what we are doing and how things are progressing.
We’ve been showing samples of the Design Development stage prototypes of our Mini-ALTO for a few months now. However, we have now moved the Mini-ALTO into the “Design Refinement” stage in preparation for full production and let’s just say this part of process has been a little tricky.
We’re using a modern process to heat-bond fabric onto a pre-moulded structure of the windshield basket & caps as well as ultra sonic welding for the joints. This massively differs to the construction of virtually all other conventional basket windshields.
The benefit of our new production process is that once made, the blimp components will act like a single solid piece of material (no noise). The dedicated mouldings make the mechanical joints stronger & much lower profile. It also makes the overall blimp much lighter. So lighter, stronger, tougher & quiet.
In our initial pre-production runs when we tested the heat-bonding of the fabric to the body, we saw incredible expansion rates of the structure material. Unfortunately, we have to compensate for this expansion by modifying the tool cavities – which means getting new tooling cut.
It's not a “back to the drawing board moment”, but a challenge that we as engineers are figuring out (and loving it). The basket body development tool is being reworked again now, and I’d expect a few more weeks before the heat bonding trials can take place again which will compensate for the heat expansion with the fabric and meet tolerances. We think this will be completed in August, and we can then complete field testing.
We will get the Mini-ALTO and ALTO right and not rush into launching products to meet arbitrary financial deadlines or marketing launch dates. As a brand we think it’s more important that our products are beaten up, tested and work as they should before handing over to customers.
Thank you to everyone in the sound community for the continued love & support. We genuinely appreciate all of the feedback & hundreds of offers of testers. Although I’d love to get all of the new products out there to test in the field as soon as possible – we will only launch them when we know they are 100% ready to go 🙏
Cheers,
Simon
Since we started Radius Windshields last year, we’ve tried to be as open as possible with the development process of our products.
One of the obvious Pro’s to our openness is that everyone can see what we are doing and how things are progressing. However…. one of the Con’s is that everyone can see what we are doing and how things are progressing.
We’ve been showing samples of the Design Development stage prototypes of our Mini-ALTO for a few months now. However, we have now moved the Mini-ALTO into the “Design Refinement” stage in preparation for full production and let’s just say this part of process has been a little tricky.
We’re using a modern process to heat-bond fabric onto a pre-moulded structure of the windshield basket & caps as well as ultra sonic welding for the joints. This massively differs to the construction of virtually all other conventional basket windshields.
The benefit of our new production process is that once made, the blimp components will act like a single solid piece of material (no noise). The dedicated mouldings make the mechanical joints stronger & much lower profile. It also makes the overall blimp much lighter. So lighter, stronger, tougher & quiet.
In our initial pre-production runs when we tested the heat-bonding of the fabric to the body, we saw incredible expansion rates of the structure material. Unfortunately, we have to compensate for this expansion by modifying the tool cavities – which means getting new tooling cut.
It's not a “back to the drawing board moment”, but a challenge that we as engineers are figuring out (and loving it). The basket body development tool is being reworked again now, and I’d expect a few more weeks before the heat bonding trials can take place again which will compensate for the heat expansion with the fabric and meet tolerances. We think this will be completed in August, and we can then complete field testing.
We will get the Mini-ALTO and ALTO right and not rush into launching products to meet arbitrary financial deadlines or marketing launch dates. As a brand we think it’s more important that our products are beaten up, tested and work as they should before handing over to customers.
Thank you to everyone in the sound community for the continued love & support. We genuinely appreciate all of the feedback & hundreds of offers of testers. Although I’d love to get all of the new products out there to test in the field as soon as possible – we will only launch them when we know they are 100% ready to go 🙏
Cheers,
Simon